IT teams oversee a wealth of critical business assets. All of the equipment that IT teams manage is central to business operations and quite valuable. Yet, a huge struggle for many IT teams is equipment inventory management.
Poor asset management can result in unnecessary equipment losses and several operational inefficiencies.
That’s why every IT team needs to manage equipment inventory. Today, we’ll share a helpful inventory management checklist for getting started.
What is Equipment Inventory?
Equipment inventory is the complete list of all of the assets you have. The equipment inventory that IT teams focus on tends to include things like:
- Desktops
- Laptops
- Printers
- Scanners
- POS systems
- Computer accessories
- Software applications
How to Inventory Assets
To inventory assets, you must implement a consistent equipment inventory system. At first, this may seem overwhelming, but in the end, it will save your team time and headache. We’ll dive into the helpful checklist for how to inventory assets, but the basic idea is to find out:
- Exactly what you have (down to the make, year, etc)
- How (and where) inventory is being used
- How to best use the inventory
- What you need
- And how to help inventory last longer
Benefits of an Equipment Inventory System
Yes, an equipment inventory list takes time to create and manage. However, it’s incredibly valuable for businesses. Here’s why you need an equipment inventory system:
- Acquire critical knowledge for smarter business decisions. Tracking all of your equipment makes it easy to understand what resources are available and what gaps in inventory may need to be filled.
- Understand equipment costs. With strong inventory management, you can easily understand the cost of equipment. This may help you determine when to replace older equipment instead of continuing to repair it.
- Preventative maintenance. It’s no secret that maintenance helps prevent equipment damage and extend its lifespan. However, it’s hard to stay on track with maintenance for all equipment without an inventory system.
- Better budgeting. The equipment usage and maintenance data can help you predict upcoming maintenance, repair, or replacement costs. This helps you create a more accurate IT budget.
- Employee accountability. Company equipment shouldn’t be a free-for-all, but keeping employees accountable is difficult. With a proper equipment management system, you can ensure greater employee accountability. You’ll know exactly who has what equipment and can carefully track sign-outs and usage. This will also help you create fair, logical policies.
- Increase efficiency. Proper inventory management makes it much quicker and easier to intake new equipment and dispose of old equipment. It also helps streamline maintenance, updates, checks, and other key equipment processes.
How to Perform a Supply Equipment Inventory
Here is a checklist for equipment inventory management:
Create an Equipment Inventory List
First and foremost, you must find out what you have. Having a complete inventory list is vital for inventory management. At first, it may be daunting to track down every piece of equipment, but once you know what you have it will be much easier to adhere to good inventory management in the future.
The list should include all assets. This includes employee-lent assets, so be sure to check with team members about the company equipment they are using (even if they work remotely). Furthermore, this list must be detailed. “Windows computer” is not enough information. Instead, each asset should include details about the make, model, year, location, and more.
Creating an equipment inventory list is not something you do once. This list must be kept up-to-date and reflect any changes. If a piece of equipment breaks beyond repair and is replaced, you must update this in the sheet. Revisit the sheet to update for any changes, and review it thoroughly at least once a year.
Track Equipment Use
Knowing what you have is only part of the battle; you also need to figure out how it’s being used. You need to know how often the equipment is used, who uses it, and the location of use. Ideally, gather this information at the same time as you build the list. Understanding equipment use will guide future decisions for equipment inventory management.
Much like the inventory list, you should update the use information regularly. If an older laptop was taken from a seasoned employee and given to an intern, you should note this change. Likewise, if Printer A moves from the break room to Susie’s cubicle, you should also update this.
Inventory Policy
Creating an equipment inventory policy will help you track, manage, and preserve inventory as much as possible. The policy should outline the role of each employee in equipment management. It should guide how employees and team members follow the inventory policy. For example, dictate the employees’ process if a computer no longer works and the IT team determines they need a new one.
Overall, establish a clear outline for equipment intake and outtake. Beyond that, you should also outline the rules for how employees should treat the equipment.
Maintenance and Warranties
Create and track maintenance schedules for the inventory. Also, keep track of the warranties for each. Automating this process can save a lot of time and streamline the process. Sticking to the outlined maintenance schedule for each asset will help prevent more time-consuming issues. By tracking this, you can also assess how much time each asset requires for maintenance and repairs, guiding decisions on updating equipment.
Use the Right System
Getting equipment inventory management in place is extremely important, but it’s not the full picture. Ultimately, you must have a strong system in place to continue to manage inventory. For example, you could opt for an equipment inventory template pdf. There are many different options available for this, but the key is to use the right system for your business.
Incorporating automated systems is extremely helpful. For example, automated point-of-sale (POS) systems help to streamline inventory management.
Get Help with Equipment Inventory Management
Tackling inventory management is a huge task, and it can be extremely difficult for IT teams to handle on their own. That’s where an experienced logistics partner can help. Working with an expert will streamline your equipment inventory management process. This saves your team a ton of time, allowing you to focus on other key projects. Many IT managers find it extremely beneficial to work with equipment inventory management experts to set up and manage their inventory systems.
Teksetra is Here to Help
Teksetra is here to help you create and implement an effective equipment inventory management system. Our experienced team provides a comprehensive range of IT, software, and hardware solutions that can help. Learn more about how we can help your team with equipment inventory management today by contacting us!
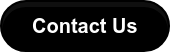